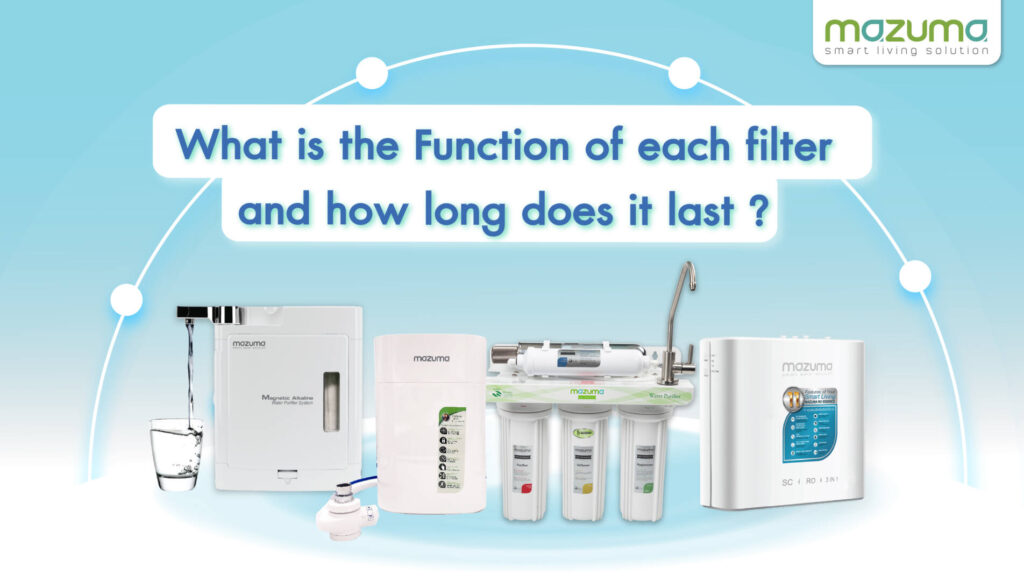
What is the function of each filter and how long does it last?
Water filters is considered to be one the most important equipment there is, because of the health issue that surounded by the enviromental in our daily lives, If we don’t use the filter it’ll not be able to filter water thoroughly and clean. The properties of the water filter will be vary and different for each type of water filter system. Most water filters on the market today are similarties depending on the quality of the filter. The filters are divided into 7 main categories, and have different characteristics Including the service life as well . We can classify the filters by their characteristics and efficiency as follows.
– ” PP filter or Sediment Filter is a coarse filter that is responsible for filtering large sediment in the water. Has a lifetime of about 6 months depending on the water conditions in each area. “
– Carbon Block filter is responsible for filtering odors, colors, chlorine in the water. There are 2 types of carbon filters which are compressed bar and pellet type.
Service life is about 6-8 months.
– Resin filter is responsible for reducing plaque build-up, hardness, and water adjustment. Service life is approximately 6-8 months.
– UF filters are responsible for filtering small sediment, chlorine, germs (some types) at a maximum resolution of 0.01 microns, without electricity and without sewage. Therefore, suitable for people who do not want to install wiring and connect the sewer system. Service life is about 1 year.
– Post Carbon filter is responsible for filtering the chlorine in the water, reducing odors, colors such as the carbon block / gas filter
used to adjust the taste of the water to be better in the final step before drinking. The service life is about 1 year.
– RO Membrane filter with a resolution of 0.0001 micron. It is a filter that combines various filters together. It can filter various contaminants and filter all necessary and unnecessary minerals to the body. Service life is approximately 24-36 months.
– UV filter (Ultra Violet) the ability to use UV light to kill germs in the water Service life is about 1 year or 7,000 hours.
– Ceramic filter Responsible for filtering bacteria at a maximum resolution of 0.3 microns, service life of about 1 year (depending on water conditions in each area) Suggestion: the filter should be changed according to the service life. Because if the filter is over due, then the filter efficiency will decrease. Should be changed for cleanliness Change for better health
15 Reviews
rgbet
rgbet RGBET – Hướng Dẫn Truy Cập Nhà Cái RGBet Chính Thức Mới Nhất 2024 Cảnh Báo Về Các Trang Web Giả Mạo RGBET.INFO Kính gửi quý khách hàng và người dùng thân mến, Chúng tôi, đại diện chính thức của [rgbet.co], muốn thông báo về một số trang web giả mạo, đặc biệt là rgbet.info, đang mạo danh RGBet nhằm đánh lừa người dùng. Chúng tôi khẳng định rằng rgbet.info không có bất kỳ liên kết nào với RGBet chính thức, và việc truy cập vào các trang này có thể gây nguy cơ cho thông tin cá nhân cũng như tài khoản của bạn. Việc giả mạo thương hiệu RGBet đã ảnh hưởng không nhỏ đến uy tín của chúng tôi và tiềm ẩn nguy cơ cho khách hàng. Những trang web này thường sẽ yêu cầu người dùng cung cấp thông tin nhạy cảm như số tài khoản ngân hàng, mật khẩu, hoặc các thông tin cá nhân khác, dễ dẫn đến mất mát tài sản hoặc dữ liệu cá nhân. Cách Nhận Biết Liên Kết Chính Thức Của RGBet Để đảm bảo sự an toàn tuyệt đối khi tham gia RGBet, khách hàng nên xác nhận rằng mình chỉ đang truy cập trang web RGBet thông qua liên kết chính thức tại [rgbet.co]. Đây là kênh duy nhất mà RGBet cung cấp để đảm bảo tính bảo mật, an toàn cho người dùng và tránh những rủi ro không đáng có. RGBet không bao giờ chuyển hướng người dùng đến trang web bên thứ ba như da88 hoặc các trang tương tự, và chúng tôi khuyến cáo bạn không nên tin tưởng những trang này. Hướng Dẫn Và Hỗ Trợ Chính Thức Từ RGBet RGBet luôn cố gắng hỗ trợ tốt nhất cho khách hàng thông qua các kênh liên lạc chính thức. Mọi thắc mắc, yêu cầu hỗ trợ hoặc vấn đề gặp phải khi truy cập có thể được giải đáp bởi đội ngũ hỗ trợ của chúng tôi. Vui lòng chỉ liên hệ thông qua các phương thức chính thức tại [rgbet.co] để đảm bảo thông tin được bảo mật. Kính mong quý khách hàng luôn cảnh giác và lựa chọn RGBet một cách an toàn và thông minh để có trải nghiệm tuyệt vời nhất. Trân trọng, Đại Diện RGBet
How is the balancing of a belt drive system conducted?
balancing equipment Balancing Equipment: Portable Balancer & Vibration Analyzer Balanset-1A Balancing Equipment: Portable Balancer & Vibration Analyzer Balanset-1A The need for precise balancing equipment in various industries is paramount for operational efficiency and equipment longevity. The Balanset-1A portable balancer and vibration analyzer is an innovative device designed to meet these requirements by providing exceptional features for dynamic balancing of different types of rotors. This multipurpose device can handle a variety of applications, making it an essential tool for industries such as manufacturing, agriculture, and energy production. Key Features of Balanset-1A The Balanset-1A is crafted with dual-channel capability, allowing it to perform dynamic balancing in two distinct planes. This unique feature enables it to accommodate a wide array of rotors—ranging from crushers and fans to augers on combines and turbines. The versatility of this balancing equipment makes it invaluable to professionals involved in rotor maintenance and analysis across various sectors. Comprehensive Functionalities This portable balancer and vibration analyzer incorporates multiple functionalities aimed at delivering outstanding performance and accuracy during vibration analysis: Vibrometer Mode: This function allows for precise monitoring of vibration levels, ensuring that the rotors operate within acceptable parameters. Tachometer: Accurately measures rotational speed in RPM, providing crucial data for balancing assessments. Phase Measurement: Determines the phase angle of vibration signals, aiding in accurate monitoring and adjustments. FFT Spectrum: The device offers detailed frequency spectrum analysis, enabling users to detect issues that may not be evident through standard measurements. Overall Vibration Monitoring: It continually tracks overall vibration levels, offering insights into rotor performance. Measurement Log: This feature saves crucial measurement data for further analysis, allowing technicians to track changes over time. Balancing Modes The device supports both single and two-plane balancing modes, thus ensuring extensive functionality for any rotor type: Single Plane Balancing: Focuses on reducing vibration in one plane for rotors that require basic balancing. Two Plane Balancing: This complex balancing mode provides dynamic stabilization for rotors requiring higher precision. Polar Graph Visualization: The Balanset-1A accurately depicts weight placements using a polar graph, greatly simplifying the process of addressing imbalances. Tolerance Calculator: Adheres to ISO 1940 standards, calculating acceptable tolerance levels for optimal balancing. Restore Last Session: Provides convenience by allowing users to easily continue from the last measurement point. Advanced Monitoring and Reporting The Balanset-1A is equipped with additional capabilities that facilitate comprehensive analysis and reporting of balancing outcomes: Charting Options: Visual representations of vibrations across different measurements help in identifying patterns and anomalies. Archived Data: Users can store past balancing sessions for easy retrieval, promoting continuous improvement and maintenance routines. Detailed Reporting: Generates reports that summarize balancing results, crucial for maintaining equipment performance standards. Serial Production Balancing: Effectively supports rotor balancing in serial production settings, enhancing operational efficiency. Specifications and Compatibility The Balanset-1A boasts powerful specifications that cement its status as a reliable piece of balancing equipment: Two Vibration Sensors with a cable length option of up to 10 meters. One Optical Sensor facilitating measurements from 50 to 500mm. USB Interface for easy connection to PCs, ensuring seamless data transfer and analysis. Compatible with both Imperial and Metric systems, allowing for global usability. Performance Metrics The performance metrics of the Balanset-1A highlight its precision and effectiveness: RMS Vibration Velocity Measurement Range: Up to 80 mm/s. Capable of measuring RPM from 250 to 90,000. Vibration Phase Shift Measurement: Comprehensive range of 0 to 360 degrees. Acceptable Measurement Error Tolerance kept to minimal levels, ensuring reliability. Conclusion In a world where precision is vital for operational success, investing in superior balancing equipment like the Balanset-1A is indispensable. Its combination of advanced technology, detailed analysis capabilities, and versatile applications makes it suitable for a broad spectrum of industries. Whether addressing the needs of crushers, fans, or complex turbine assemblies, the Balanset-1A stands out as a top-tier portable balancer and vibration analyzer, ensuring effective maintenance and optimal rotor performance for years to come. Article taken from https://vibromera.eu/
Machine balancing
dynamic balancing Dynamic balancing is essential for maintaining the operational efficiency of various machinery components that involve rotational motion. Achieving a well-balanced rotor significantly reduces vibrations and enhances the lifespan of equipment, making it a fundamental process across numerous industries. In this text, we delve into the intricacies of dynamic balancing, particularly focusing on the use of modern devices and established techniques to correct imbalances in rotors. To fully understand dynamic balancing, it is crucial to differentiate it from static balancing. Static imbalance occurs when a rotor is stationary, resulting in its center of gravity being displaced from the axis of rotation. This leads to an uneven distribution of mass that causes one side to become heavier, forcing the rotor to reposition itself to bring the heavy point downward. Static balancing techniques are generally applied to narrow, disk-shaped rotors to redistribute mass within a single plane. In contrast, dynamic imbalance arises when the rotor is in motion. It entails mass displacement in multiple planes, resulting in both axial forces and additional moments that create vibrations. Dynamic balancing is necessary when imbalances occur due to differential mass distributions along the length of a rotating shaft. Correcting dynamic imbalance requires an accurate vibration analyzer that can account for forces in two separate planes. The combination of these factors makes dynamic balancing critical for longer rotors, effectively addressing the need for balance across multiple planes to prevent vibration during rotation. The instruction for dynamic shaft balancing involves using a state-of-the-art portable device known as Balanset-1A. This versatile device features two channels, allowing it to perform dynamic balancing in two planes effectively. It can be utilized across a wide array of applications, including crushers, fans, centrifuges, and turbine systems. The Balanset-1A is indispensable in various industries due to its ability to handle different rotor types and sizes. The dynamic balancing process begins by measuring the initial vibration of the rotor while it is mounted on the balancing machine. Vibration sensors are connected to the rotor and data is collected to establish a baseline for subsequent measurements. This initial phase is vital, as it informs the operator of the rotor’s existing condition and prepares them for adjustments. Once the baseline is established, a calibration weight is introduced. During the second stage, this known mass is installed at an arbitrary point on the rotor to observe its effects on vibration. The rotor is restarted, and the system records any changes in vibration levels due to this additional weight. By moving the calibration weight to different points on the rotor and measuring the resulting vibrations, operators can gather crucial data to inform them about the necessary adjustments. The final stage of dynamic balancing involves calculating the corrective weights based on the vibration data recorded from both planes. Using the analysis tools embedded within the Balanset-1A, operators can determine the precise mass and location of the corrective weights required to achieve optimal balance. After installing these weights, a final measurement is taken to confirm whether the adjustments have successfully minimized vibrations to acceptable levels. Furthermore, the process of measuring angles for corrective weight installation is integral to effective dynamic balancing. The angles indicate the precise positioning needed for any added mass. By understanding these angles, operators can ensure that the corrective weights are placed accurately, further increasing the likelihood of achieving balance and reducing vibrations in the rotor. Looking closely at the calculations for the trial weight's mass, understand that they play a key role in dynamic balancing. This complexity emphasizes the precision required in selecting trial weights as well as ensuring their placement in accordance with the rotor's speed and structural attributes. This calculation promotes an exact, strategic approach to achieving balance, allowing for the best results with minimal trial and error. Moreover, the dynamic balancing process highlights the need for appropriate installation locations for vibration sensors. These sensors collect vibration data needed for analysis and adjustments, making their placement essential in the balancing equation. The Balanset-1A gadget shows flexibility in balancing procedures by allowing for multiple sensor installations, which further enhances the accuracy of the data collected. Two-plane dynamic balancing is particularly important for applications like fans, where identifying correction planes and actual sensor placements can directly affect performance. Effective vibration measurement, placement of trial weights, and analysis of collected data guarantee that the balancing process is both thorough and effective. In conclusion, mastering dynamic balancing processes is a critical factor for ensuring operational efficiency and extending equipment lifespan in numerous industries. Whether through the use of devices like the Balanset-1A or the implementation of mechanical techniques, achieving a dynamically balanced rotor mitigates unacceptable vibrations, enhancing performance. This discipline not only contributes to smoother operation but also supports preventive maintenance strategies, ultimately leading to lower operational costs and increased reliability. As industries continue to evolve, the importance of dynamic balancing remains a consistent requirement for optimizing the performance of machinery. Article taken from https://vibromera.eu/
Rotary analysis
static balancing Static Balancing: The Key to Efficient Rotors Static balancing is an essential process in the maintenance of various rotating machinery. Understanding the concept of static balancing can enhance the efficiency and performance of engines, fans, crushers, and other machines with rotors. This balancing method addresses uneven mass distribution, ensuring smooth operation and reducing the risk of wear or damage during service. What is Static Balancing? Static balancing occurs when a rotor is stationary. In this state, the center of gravity of the rotor is not aligned with its axis of rotation. This imbalance creates a tendency for the rotor to tilt or shift, causing one side to be heavier than the other. As a result, the "heavy point" of the rotor will consistently rotate downward under the influence of gravity, which can lead to vibration and wear if left unchecked. The Importance of Static Balancing Static balancing is particularly critical for narrow, disk-shaped rotors, which often require precision in mass distribution. By eliminating uneven mass distribution in one plane, static balancing not only improves the operational stability of these components but also extends their lifespan. A well-balanced rotor reduces the strain on bearings and other supporting structures, ultimately leading to lower maintenance costs and better performance efficiency. Static vs. Dynamic Balancing While both static and dynamic balancing aim to correct imbalances in rotors, they do so in different contexts. Static imbalance occurs when the rotor is at rest, allowing straightforward corrective actions based on gravitational forces. In contrast, dynamic balancing becomes relevant when the rotor is in motion, dealing with more complex scenarios where uneven mass distributions exist across multiple planes. How Static Balancing is Achieved The process of static balancing involves several straightforward steps. Initially, the rotor is mounted on a balancing machine, where technicians can identify the heavy points. Once identified, corrective weights are added or removed to ensure the center of gravity aligns with the axis of rotation. This process may require multiple adjustments and measurements before achieving perfect balance. Static Balancing Techniques Various techniques can be employed to achieve static balancing effectively. The most common method involves attaching or detaching weights at specific locations on the rotor until the desired balance is reached. Technicians might also use software tools that calculate the required weight adjustments based on vibration analysis. The emphasis is always on precise adjustments to minimize residual vibrations during operation. Benefits of Static Balancing When applied correctly, static balancing results in significant benefits for any rotor-based machinery: Improved Efficiency: With balanced rotors, equipment can run more smoothly, which leads to better energy efficiency and reduced operational costs. Extended Lifespan: Reducing wear and strain on mechanical components extends the lifespan of the machinery, thus optimizing investment over the long run. Enhanced Safety: Balanced rotors decrease the likelihood of machine failure, leading to safer operational conditions for personnel. Less Vibration: A well-balanced rotor minimizes vibrations, which in turn limits noise pollution and improves working conditions. Precision Operations: In industries where precision is key, static balancing ensures optimal performance, preventing costly deviations during production. Applications of Static Balancing Static balancing is widely applicable across different industries. Here are some notable applications: Manufacturing: In production facilities where machinery operates continuously, static balancing ensures that machines like fans and motors run efficiently. Aerospace: The aerospace industry relies on precision; static balancing contributes to the performance of engines, rotors, and other crucial components. Automotive: Engine components like crankshafts benefit from static balancing, which enhances performance and fuel efficiency. HVAC Systems: Fans and blowers used in air conditioning systems require static balancing to minimize noise and energy consumption. Power Generation: Turbines and generators must undergo static balancing to operate reliably and efficiently, impacting overall power generation capacity. Static Balancing Equipment Utilizing the right tools is essential for effective static balancing. Devices such as portable balancers and vibration analysis units can aid technicians in accurately measuring and correcting imbalances. Equipment like the Balanset-1A offers multi-plane balancing capabilities essential for evaluating the rotor’s balance status, making it easier to implement corrective actions with precision. Choosing the Right Balancer When selecting a balancing device, it is crucial to consider factors such as accuracy, versatility, and ease of use. A quality balancer will allow operators to perform measurements efficiently, ensuring that static balancing can be achieved promptly and effectively. Look for products that have established reputations in the industry for reliability and performance. Conclusion Static balancing is a crucial aspect of maintaining the integrity and performance of rotating machinery. Whether in industrial applications or specialized fields like aerospace and manufacturing, understanding and implementing static balancing can lead to substantial gains in efficiency and equipment longevity. By investing in the right tools and embracing best practices for static balancing, companies can enhance operation efficiency and achieve significant long-term savings. Don't underestimate the impact of static balancing on your operations—ensure that your machinery performs at its best by keeping your rotors perfectly balanced! Article taken from https://vibromera.eu/
Хрумер Обучение
Хрумер Обучение Kwork Overview Обучаю делать ссылочную массу на сайт или социальную сеть програмным обеспечением XRumer. В обучение входит Настройка Xрумера для работы в режиме постинг Покажу сайты где брать прокси, VPS сервис Свожу баланс (оптимизирую) хрумер, ксевил и сервер, для эффективной работы. Работаю на 6-й версии ксевила План такой! Устанавливаем XRumer на удалённый сервер (личный компьютер не подходит для работы) Показываю настройки для работы и составление проекта Постинг будет производиться в блоги и коментарии, форумы не использую по причине модерации и жалоб от модераторов, поэтому настройку почты не делаю Сбор базы в обучение не входит.